


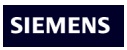


Sterilization In Place
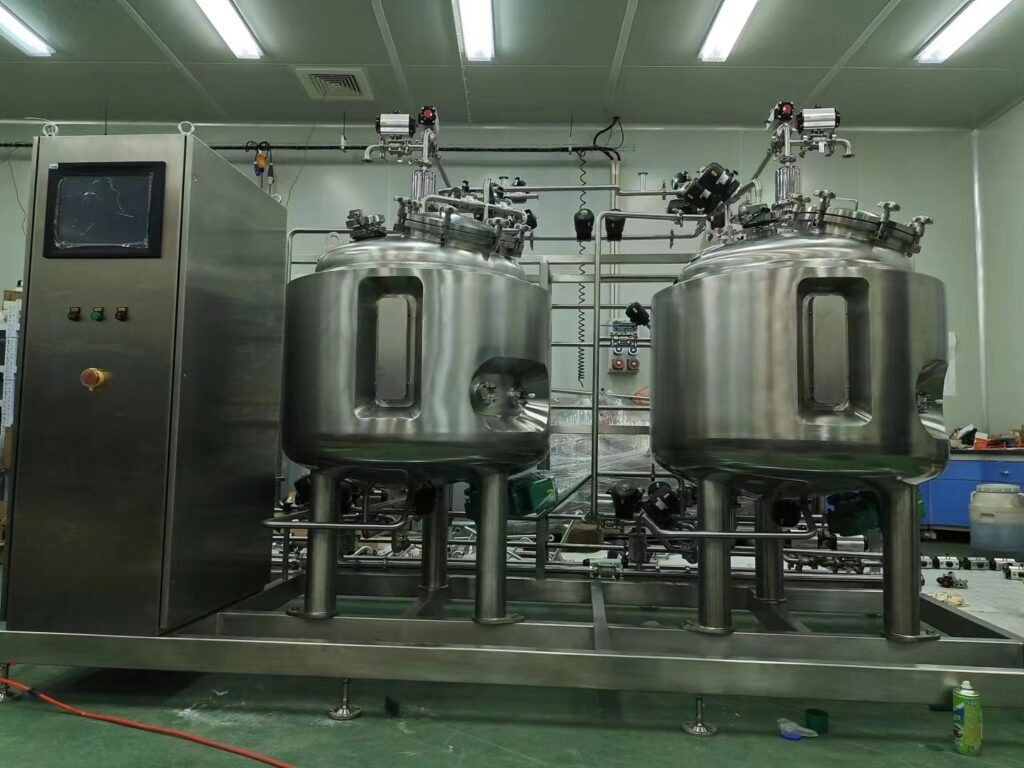
In the pharmaceutical industry, SIP stands for Sterilization in Place. It is a process used to sterilize the internal surfaces of equipment and piping in manufacturing facilities without having to disassemble them. SIP is a critical step in ensuring that the production of pharmaceutical products is carried out in a sterile environment, which is essential for maintaining the safety and efficacy of the products.
Key Aspects of SIP:
- Sterilization Method: Typically, SIP is achieved using steam or other sterilizing agents like chemicals, which are circulated through the equipment at high temperatures. Steam is the most common method due to its effectiveness in killing microorganisms.
- Application Areas: SIP is used in various parts of the pharmaceutical manufacturing process, including tanks, reactors, pipelines, and filling lines. Any equipment that comes into direct contact with the product may require SIP.
- Automation: The SIP process is usually automated to ensure consistency and reliability. The parameters such as temperature, pressure, and time are carefully controlled to meet the required sterilization standards.
- Validation: SIP processes must be validated to ensure they are effective in sterilizing the equipment. This involves rigorous testing and documentation to confirm that the process consistently meets regulatory standards.
- Regulatory Compliance: SIP is a critical aspect of Good Manufacturing Practice (GMP) and is required by regulatory bodies like the FDA and EMA. Proper SIP ensures that the pharmaceutical products are free from contaminants, which is essential for patient safety.
SIP components:
1. Steam Source
- Steam Generator or Boiler: Provides the steam required for sterilization. The steam must be pure (often termed as clean steam) and free from contaminants to ensure it doesn’t introduce impurities into the equipment being sterilized.
2. Piping and Valves
- Sterile Piping: The system of pipes that distributes steam throughout the equipment. The piping must be designed to avoid dead legs where steam could stagnate, as these areas can become sources of contamination.
- Sterile Valves: Special valves are used to control the flow of steam and vent condensate. These valves are designed to be hygienic and to minimize the risk of contamination.
3. Control System
- Automation and Control Unit: Monitors and controls the SIP process, including parameters such as steam pressure, temperature, and sterilization time. It ensures the process runs according to pre-set, validated cycles.
- Sensors and Instrumentation: These include temperature sensors, pressure sensors, and flow meters that provide real-time data to the control system, ensuring that the sterilization process is maintained within the required parameters.
4. Condensate Removal System
- Traps and Drains: Steam traps and drains are used to remove condensate (water formed when steam cools) from the system, ensuring that only dry, saturated steam comes into contact with the surfaces being sterilized.
5. Sterilization Chamber or Equipment
- Process Vessels and Equipment: This includes the tanks, reactors, fermenters, and any other equipment that requires sterilization. The design of these vessels must facilitate even steam distribution and effective condensate removal.
- Filling Lines and Tubing: For systems that include product contact surfaces, such as filling lines, tubing, and pumps, these components must be included in the SIP cycle.
6. Ventilation and Vacuum Systems
- Vacuum System: Some SIP systems include a vacuum to remove air from the equipment before steam is introduced. This helps ensure uniform steam distribution and effective sterilization.
- Vent Filters: These are used to filter air that is vented out of the system during sterilization, preventing contamination.
7. Drainage and Waste Handling
- Sterile Drains: Drains must be designed to handle the discharge of sterilized condensate or other fluids without risking recontamination. These drains are connected to sterile piping systems to prevent contamination from outside sources.
8. Documentation and Validation Tools
- Data Logging: Systems that record the parameters of each sterilization cycle for validation and regulatory compliance.
- Validation Ports: Ports or connections that allow for the introduction of biological indicators or sensors for validation purposes.
9. Auxiliary Equipment
- Chemical Injection Systems (if chemical sterilization is used): For injecting sterilizing agents other than steam, such as hydrogen peroxide or peracetic acid.
- Gaskets and Seals: All gaskets and seals in the system must be designed to withstand the sterilization process and prevent leaks or contamination.