


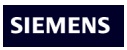


Mixing Tank

A mixing tank in pharmaceutical manufacturing is a vessel designed for the homogeneous blending of liquids, powders, and other ingredients. It is typically made from high-grade stainless steel, such as SS316L, to prevent contamination and ensure easy cleaning. The tank is equipped with an agitator or mixer that ensures consistent mixing throughout the process. Temperature control systems, such as jackets or coils, are often included to maintain the desired temperature during mixing. The mixing tank is crucial in ensuring uniformity in product formulations, meeting strict pharmaceutical quality standards. It is widely used in the preparation of solutions, suspensions, and emulsions in pharmaceutical production.
Mixing Tank Design Features:
Composition
- Tank Body: Typically constructed from high-grade stainless steel (SS304 or SS316L) to resist corrosion, maintain hygiene, and ensure durability. The inner surface is often polished to a mirror finish to prevent contamination and facilitate easy cleaning.
- Agitator/Mixer: Located inside the tank, this mechanical device, which could be a propeller, turbine, or anchor type, is responsible for stirring the contents. It ensures that all ingredients are evenly mixed, preventing sedimentation or stratification.
- Jacket/Coils: External heating or cooling jackets, or internal coils, allow precise temperature control within the tank, which is essential for processes that require specific temperature conditions during mixing.
- Baffles: Internal vertical plates (baffles) are often installed to disrupt the flow pattern and improve mixing efficiency, particularly in large tanks.
- Sensors and Control System: Integrated sensors monitor critical parameters such as temperature, pH, and viscosity, while the control system (often PLC-based) automates and optimizes the mixing process.
- Outlet Valve: A sanitary valve at the bottom of the tank ensures efficient discharge of the mixed product, minimizing residue and waste.
Process
- Loading: Ingredients, such as liquids, powders, or gases, are loaded into the tank through designated inlets.
- Mixing: The agitator is activated, stirring the contents at a controlled speed to achieve uniform mixing. The duration and speed of mixing are adjusted based on the specific product formulation.
- Heating/Cooling: If required, the temperature of the tank contents is controlled through the jacket or coils to facilitate chemical reactions or to achieve the desired viscosity.
- Sampling: Samples may be taken during or after mixing to ensure the mixture meets the required specifications.
- Discharge: Once the mixing process is complete, the mixture is discharged through the outlet valve, typically into downstream processing equipment or containers.
Performance
- Mixing Efficiency: The design of the agitator, baffles, and tank geometry ensures thorough mixing, achieving a homogenous blend even for complex formulations.
- Temperature Control: The system maintains precise temperature control, crucial for processes that require heating or cooling during mixing.
- Scalability: Mixing tanks are available in various sizes, from small laboratory-scale units to large industrial tanks, making them versatile for different production volumes.
- Hygienic Design: The use of sanitary materials and finishes, combined with easy-to-clean designs, ensures that the mixing tank meets the strict hygiene standards required in pharmaceutical manufacturing.
- Process Automation: The inclusion of advanced control systems enables automation of the mixing process, ensuring consistency, reducing human error, and improving operational efficiency.
Applications
- Pharmaceutical Manufacturing: Used for blending active pharmaceutical ingredients (APIs) with excipients, preparing solutions, suspensions, emulsions, and other dosage forms.
- Biotechnology: Employed in the preparation of culture media, buffer solutions, and other biotech products.
- Food and Beverage: Utilized for mixing ingredients in the production of food, beverages, and nutraceuticals under stringent hygiene conditions.
The mixing tank is essential in ensuring the uniformity and quality of products in pharmaceutical production, supporting a wide range of mixing processes with high efficiency and reliability.