


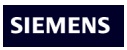


Clean In Place
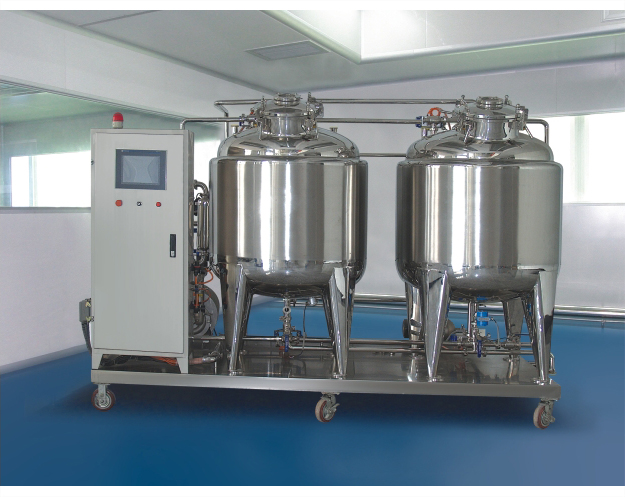
Clean In Place (CIP) in pharmaceutical equipment is an automated process that cleans the interior surfaces of pipes, vessels, and equipment without disassembly. It works by circulating cleaning agents—such as water, detergents, and sanitizers—through the system in a controlled sequence. The process typically involves multiple stages, including pre-rinse, detergent wash, post-rinse, and sanitization. CIP systems are designed to ensure thorough cleaning by maintaining precise control over time, temperature, flow rate, and chemical concentration. The principle behind CIP is to achieve consistent, repeatable cleaning that meets stringent hygiene standards. This method ensures equipment is free from contaminants, supporting sterile and safe pharmaceutical production.
Clean In Place Features:
Composition
- CIP Skid: The central unit housing tanks, pumps, valves, and control systems. It includes separate tanks for storing cleaning agents, detergents, and rinse water, as well as heating elements to control temperature.
- Pumps: High-efficiency pumps circulate cleaning solutions through the system, ensuring adequate flow and pressure for effective cleaning.
- Valves and Piping: Automated valves and sanitary piping direct the flow of cleaning agents to specific areas of the equipment, ensuring coverage of all internal surfaces.
- Control System: A PLC-based system automates the entire CIP process, including monitoring and controlling flow rates, temperatures, and cleaning cycle durations. It also records data to ensure compliance with regulatory standards.
- Instrumentation: Sensors measure critical parameters such as temperature, flow rate, and chemical concentration, ensuring the cleaning process meets predefined specifications.
Process
- Pre-Rinse: The system initiates with a pre-rinse using water to remove loose residues from the equipment’s surfaces.
- Detergent Wash: A detergent solution is circulated through the equipment to dissolve and remove organic and inorganic contaminants.
- Post-Rinse: Following the detergent wash, the system rinses the equipment with water to remove any residual cleaning agents.
- Sanitization: A sanitizing agent or high-temperature rinse is applied to eliminate microbial contamination, ensuring sterile equipment.
- Final Rinse: A final rinse with purified water ensures no traces of cleaning chemicals remain, leaving the equipment ready for use.
Performance
- Efficiency: CIP systems offer fast and efficient cleaning cycles, reducing equipment downtime and increasing production capacity.
- Consistency: Automated control systems ensure repeatable, high-quality cleaning results, maintaining consistent standards across batches.
- Safety: CIP reduces the need for manual cleaning, minimizing the risk of contamination and operator exposure to cleaning agents.
- Compliance: CIP systems are designed to meet stringent regulatory requirements, such as cGMP, FDA, and other industry standards, ensuring that all cleaning processes are properly documented and validated.
- Customization: The system can be tailored to specific needs, including the choice of cleaning agents, cycle duration, and temperature, to suit different types of equipment and residues.
Applications
- Pharmaceutical Manufacturing: Ensures sterile production environments for the manufacture of drugs, vaccines, and other pharmaceutical products.
- Biotechnology: Maintains the cleanliness of equipment used in the production of biopharmaceuticals, where contamination control is critical.
- Food and Beverage: Ensures the hygienic processing of food products by effectively cleaning and sanitizing production equipment.
CIP systems are essential for maintaining the hygiene and operational efficiency of pharmaceutical equipment, ensuring that manufacturing processes meet the highest standards of cleanliness and safety.