Introduction
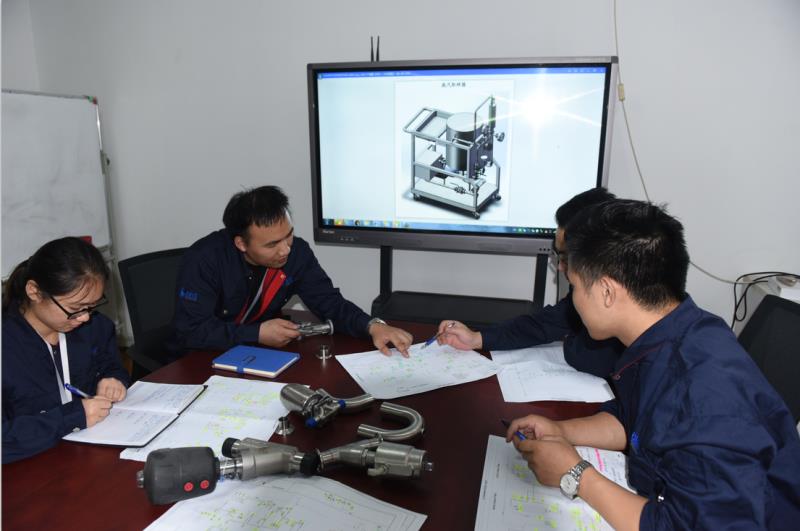
The design of pharmaceutical purified water equipment is crucial for ensuring the consistent production of high-purity water that meets industry regulations. Proper design helps maintain water quality, reduces contamination risks, and supports efficient operation. This article explores the key design requirements for pharmaceutical purified water systems.
1. Compliance with Regulatory Standards
1.1. cGMP and GMP Compliance
- Hygienic Design: Equipment must adhere to cGMP/GMP guidelines, ensuring all components are easily cleanable and sterilizable.
- Documentation: Comprehensive documentation and validation processes are essential to demonstrate compliance.
1.2. FDA and USP Standards
- Material Compliance: All materials used in the equipment must meet FDA and USP standards, ensuring safety and non-reactivity.
- Water Quality Specifications: The design must support the production of water that meets USP standards for Purified Water (PW) or Water for Injection (WFI).
2. Hygienic and Sanitary Design
2.1. Smooth Surface Finishes
- Surface Roughness: Internal surfaces should have a smooth finish (typically Ra ≤ 0.8 µm) to minimize microbial growth and facilitate cleaning.
- Crevice-Free Design: Avoiding dead legs and crevices in the design prevents microbial contamination and biofilm formation.
2.2. Sterilization Capabilities
- CIP/SIP Systems: Incorporate Clean-In-Place (CIP) and Steam-In-Place (SIP) systems to ensure thorough cleaning and sterilization without disassembly.
- Temperature Control: Design must support controlled temperatures for effective sterilization and microbial control.
3. Material and Component Selection
3.1. Corrosion-Resistant Materials
- Stainless Steel Use: 316L stainless steel is commonly used for its corrosion resistance and durability.
- High-Grade Polymers: Consider PVDF or PTFE for components exposed to aggressive chemicals or high temperatures.
3.2. Gasket and Seal Selection
- Material Compatibility: Use FDA-compliant gaskets and seals, such as EPDM or PTFE, that are resistant to chemicals and high temperatures.
- Leak Prevention: Ensure proper sealing to prevent leaks and contamination.
4. System Efficiency and Reliability
4.1. Energy Efficiency
- Pump and Motor Design: Select energy-efficient pumps and motors to reduce operational costs and environmental impact.
- Heat Recovery: Consider integrating heat recovery systems to optimize energy use.
4.2. Redundancy and Backup Systems
- Critical Components: Design should include redundancy for critical components like pumps, membranes, and UV systems to ensure continuous operation.
- Alarm Systems: Incorporate alarms and monitoring systems to detect issues early and prevent system downtime.
5. Flexibility and Scalability
5.1. Modular Design
- Scalability: Design equipment with a modular approach, allowing for easy expansion as water demand increases.
- Customization: Ensure the system can be customized to meet specific user requirements and integrate with existing infrastructure.
5.2. Flexible Operation
- Automation: Include automation features that allow for flexible operation, monitoring, and control.
- Adjustable Flow Rates: Design should accommodate varying flow rates and production volumes.
Conclusion
The design of pharmaceutical purified water equipment must prioritize regulatory compliance, hygienic operation, material selection, efficiency, and scalability. By adhering to these design requirements, manufacturers can ensure the production of high-purity water that meets the stringent needs of the pharmaceutical industry.