


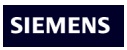


Storage and Distribution System

The storage and distribution system in pharmaceutical water treatment ensures that purified water retains its quality until use. It provides a consistent and reliable supply of water to various points in the facility, essential for continuous production. The system adheres to regulatory standards like cGMP and FDA, ensuring compliance. Its design prevents biofilm formation and contamination, maintaining water integrity. Customization options allow the system to meet specific operational needs. Overall, it plays a critical role in preserving water quality and supporting pharmaceutical manufacturing processes.
Composition:
- Storage Tanks: Made of high-grade stainless steel (typically SS316L) with sanitary finishes, these tanks store purified water while minimizing contamination risks. They often include features like vent filters, level sensors, and spray balls for CIP (Clean-in-Place) systems.
- Distribution Loop: A closed-loop system that circulates purified water throughout the facility, ensuring it remains within specification until it reaches the point of use. This loop is typically constructed from sanitary stainless steel piping with orbital welding to prevent contamination.
- Pumps: Sanitary pumps with low shear designs are used to circulate water through the distribution loop without compromising its quality.
- Filtration Units: Final filters are installed before critical points of use to remove any potential contaminants that might have entered the system.
- Control Systems: Automated control panels equipped with PLCs (Programmable Logic Controllers) manage the system’s operation, monitoring parameters like flow rate, pressure, temperature, and conductivity.
Performance
- High Purity Maintenance: The system is designed to maintain the purity of the water by preventing microbial growth and contamination. It often includes UV sterilizers or ozone systems for periodic sanitization.
- Continuous Circulation: The distribution loop ensures continuous water movement, preventing stagnation, which could lead to microbial growth or biofilm formation.
- Temperature Control: The system is equipped to maintain water at a specified temperature, critical for processes requiring temperature-sensitive water.
Parameters
- Flow Rate: Customizable based on facility needs, with typical systems supporting a range from a few liters per minute to several hundred liters per minute.
- Pressure: The system is designed to maintain stable pressure throughout the distribution loop, generally between 2-6 bar, depending on the process requirements.
- Conductivity: Monitored to ensure water quality, with typical values maintained below 1.3 µS/cm (depending on the purity requirements).
- Temperature: The system can maintain water at controlled temperatures, often in the range of 20-85°C, depending on the specific pharmaceutical process needs.