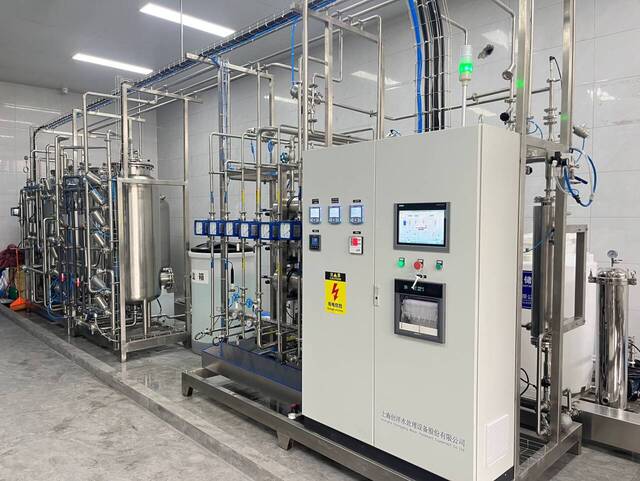
If you are buying an pharmaceutical water system for the first time and have been thinking about
How to understand and choose an pharmaceutical water system ,we hope this article can provide you with some useful help and insights .
We believe that if you read these contents carefully,you will have systematic understanding of the Pharmaceutical water system .
RESOURCES
- Understanding URS for Pharmaceutical Purified Water Equipment: Discover what a User Requirement Specification (URS) entails for pharmaceutical purified water systems.
- Key Elements in a URS: Learn about the essential components that should be included in a URS to ensure comprehensive equipment specifications.
- Global Standards for Pharmaceutical Water: Review the pharmaceutical water standards across various countries and understand the regulatory requirements.
- Processes of Pharmaceutical Purified Water Production: Explore the detailed processes involved in producing pharmaceutical-grade purified water.
- Impact of Source Water Quality on Treatment Processes: Understand why varying qualities of source water necessitate different water treatment processes.
- Customization of Pharmaceutical Purified Water Systems: Find out how these systems can be tailored to meet specific production needs and standards.
- Microorganism Control in Pharmaceutical Purified Water: Learn strategies for effectively controlling microbial contamination in purified water.
- Sterilization Techniques for Pharmaceutical Purified Water: Delve into the methods used to sterilize pharmaceutical purified water, ensuring safety and compliance.
Table of Contents
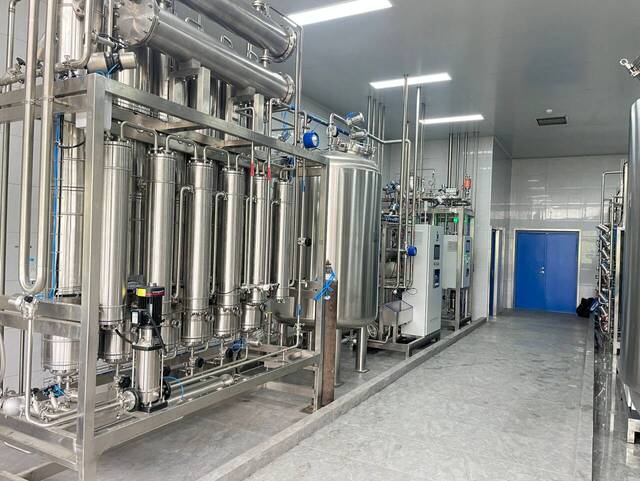
In this section, we delve deep into the sophisticated processes that ensure the highest quality of pharmaceutical-grade water. You’ll gain comprehensive insights into our advanced multi-effect distillation systems, designed to meet stringent global standards.
RESOURCES
- Types of Distilled Water Machines: An overview of the various distilled water machines available, tailored for different pharmaceutical applications.
- Composition of Multi-Effect Distillation Equipment: Delve into the components that make up multi-effect distillation systems, essential for high-purity water production.
- Endotoxin Removal Capabilities: Understand whether and how stills can be utilized to remove endotoxins effectively from water.
- Operational Mechanics of a Still: Explore how a still operates to produce distilled water, focusing on the technology behind the process.
- Utility System Requirements for Stills: Learn about the necessary conditions and support systems required for optimal still operation.
- Control Requirements of Stills: Examine the specific control standards and mechanisms essential for the efficient and safe operation of stills.
- Hot-Press Water Distillers Explained: Discover what makes hot-press water distillers unique and how they fit into the landscape of water distillation technology.
- Ultrafiltration for Water for Injection: Discuss the potential of ultrafiltration membranes in producing water for injection and their effectiveness compared to traditional methods.
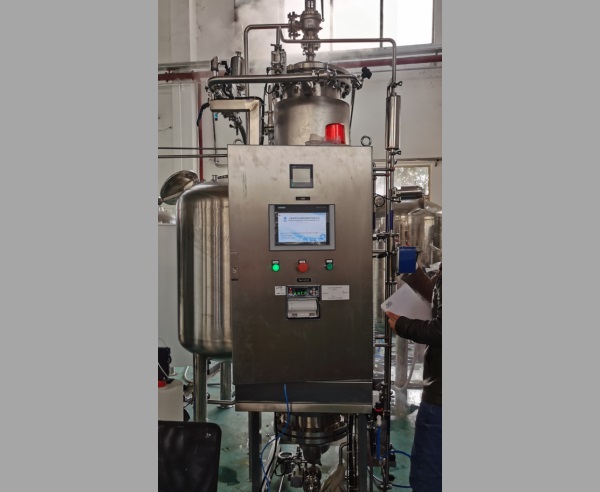
This section explores the integral role of pure steam generators in achieving wet heat sterilization and the disinfection of equipment and piping systems. Understand the mechanisms, applications, and operational standards essential for maintaining high-level cleanliness and compliance in pharmaceutical environments.
RESOURCES
Understanding the Principles of Pure Steam Generators: Explore the fundamental workings of pure steam generators, detailing their design and functionality within pharmaceutical water systems.
Applications of Pure Steam Generators: Learn about the diverse applications of pure steam generators, from sterilization processes to ensuring the cleanliness of critical equipment and piping.
Testing and Quality Indices for Pure Steam Generators: Dive into the standards and tests essential for evaluating the performance and compliance of pure steam generators in the pharmaceutical industry.

In this section, we delve into the intricacies of storage and distribution systems within pharmaceutical water systems. You’ll gain insights into how these systems are designed to maintain water purity, ensure seamless delivery, and comply with rigorous health and safety standards.
RECOURCES
- Function of Storage and Distribution in Pharmaceutical Purified Water Systems: Explore the essential role of storage and distribution functions in maintaining the purity and availability of pharmaceutical water.
- Design Concepts of Distribution Systems: Learn about the principles and strategies that guide the design of effective water distribution systems in pharmaceutical settings.
- Types of Storage Tanks: Discover the different types of storage tanks used in pharmaceutical water systems, each tailored to specific storage needs and standards.
- Components of Pipeline Distribution Systems: Delve into the various components that make up pipeline distribution systems, understanding how each part contributes to efficient water transport.
- Disinfection Methods for Tank and Piping Systems: Review the methods and technologies used to disinfect tanks and pipelines, ensuring water safety and compliance with health regulations.
Guideline on Water For Pharmaceutical Use EMEA
What is the content of USR of Pharmaceutical Water System ?
What is the influence of source water quality on the process of water treatment equipment?
A well-defined User Requirement Specification (URS) is essential for ensuring that a pharmaceutical water treatment system meets the specific needs and regulatory standards of the facility. Below are the key components that should be included in a URS:
1. General Information
- Purpose of the System: Clearly define the purpose and intended use of the water treatment system within the pharmaceutical manufacturing process.
- Location and Installation: Specify the location where the system will be installed and any site-specific requirements.
2. Performance Requirements
- Water Quality Standards: Detail the required water quality standards, such as USP, EP, JP, or other relevant pharmacopoeia standards.
- Contaminant Levels: Define acceptable levels for various contaminants including microbial counts, endotoxins, and chemical impurities.
- Capacity and Flow Rates: Specify the required production capacity (e.g., liters per hour) and flow rates.
- Recovery Rates: Indicate the desired recovery rates for the system.
3. System Components
- Type of System: Identify the type of system needed (e.g., Reverse Osmosis System, Purified Water System, Water for Injection Machine, Pure Steam Generator).
- Materials of Construction: Specify the materials to be used, particularly for components in contact with water (e.g., stainless steel 316L).
- Automation and Control: Describe the level of automation required, including control systems, monitoring, and data logging capabilities.
4. Regulatory and Compliance Requirements
- Standards and Guidelines: List all applicable standards and guidelines, such as FDA, cGMP, GMP, and other regional regulatory requirements.
- Documentation: Define the required documentation, including validation protocols, standard operating procedures (SOPs), and user manuals.
5. Operational Requirements
- Start-up and Shut-down Procedures: Detail the procedures for system start-up, operation, and shut-down.
- Maintenance Requirements: Specify the maintenance protocols, including frequency and type of maintenance required.
- Training: Indicate the need for operator training and any specific training requirements.
6. Environmental and Utility Requirements
- Utility Connections: Define the requirements for utility connections such as water, electricity, and drainage.
- Environmental Conditions: Specify the environmental conditions under which the system will operate, including temperature and humidity ranges.
7. Safety and Risk Management
- Safety Features: Describe the necessary safety features and interlocks to prevent accidents and ensure safe operation.
- Risk Assessment: Include a risk assessment to identify potential hazards and mitigation strategies.
8. Testing and Validation
- Factory Acceptance Testing (FAT): Define the requirements for FAT to be performed before the system is shipped.+
- Site Acceptance Testing (SAT): Specify the requirements for SAT to be performed after installation.
- Validation Requirements: Outline the validation requirements, including Installation Qualification (IQ), Operational Qualification (OQ), and Performance Qualification (PQ).
The quality of source water has a significant impact on the efficiency and effectiveness of pharmaceutical water treatment processes. Here are the key aspects of how source water quality influences the treatment equipment:
1. Pretreatment Requirements
- High Levels of Suspended Solids: If the source water has high turbidity or suspended solids, more robust filtration and sedimentation processes are needed to prevent clogging and fouling of downstream equipment.
- Hardness: Water with high hardness (calcium and magnesium ions) requires effective softening to prevent scaling in reverse osmosis membranes and other equipment.
2. Reverse Osmosis (RO) System Performance
- Dissolved Solids: High levels of dissolved solids (TDS) in source water can reduce the efficiency of RO membranes, leading to frequent membrane fouling and the need for more intensive cleaning and maintenance.
- Chlorine and Chloramines: These disinfectants can damage RO membranes, necessitating the use of dechlorination steps (e.g., activated carbon filters) before the RO process.
3. Electrodeionization (EDI) Efficiency
- Conductivity: Source water with high conductivity requires more energy and may reduce the lifespan of EDI components. Proper pretreatment is essential to ensure low conductivity water enters the EDI units.
- Organic Compounds: Organic contaminants can affect the ion exchange resins used in EDI, requiring additional pretreatment such as activated carbon adsorption.
4. Storage and Distribution System Integrity
- Microbial Content: High microbial content in source water can lead to biofilm formation in storage tanks and distribution pipelines, compromising water quality and requiring more rigorous sanitization protocols.
- Chemical Stability: Variability in the chemical composition of source water can affect the stability of treated water, necessitating precise control and monitoring.
5. Overall System Maintenance and Longevity
- Fouling and Scaling: Poor source water quality accelerates fouling and scaling in various system components, increasing maintenance frequency and costs, and potentially shortening the lifespan of the equipment.
- Corrosion: Source water with corrosive properties (e.g., low pH or high salinity) can damage pipes, tanks, and other system components, requiring the use of corrosion-resistant materials and coatings.
Ensuring Optimal Source Water Quality
To mitigate these impacts, it is crucial to:
- Conduct a thorough analysis of source water quality before designing the treatment system.
- Implement appropriate pretreatment processes tailored to the specific characteristics of the source water.
- Regularly monitor source water quality and adjust treatment processes as needed.
What are the standards for pharmaceutical water in each country?
Here is a table summarizing the standards for pharmaceutical water in various countries, highlighting key parameters such as conductivity, total organic carbon (TOC), and microbial limits.
Country/Region | Standard | Water Type | Conductivity (µS/cm) | TOC (ppb) | Microbial Limits (CFU/mL) | Endotoxins (EU/mL) |
United States | USP (United States Pharmacopeia) | Purified Water (PW) | ≤ 1.3 (25°C) | ≤ 500 | ≤ 100 | N/A |
Water for Injection (WFI) | ≤ 1.1 (20°C) | ≤ 500 | ≤ 10 | ≤ 0.25 | ||
European Union | EP (European Pharmacopoeia) | Purified Water (PW) | ≤ 4.3 (20°C) | ≤ 500 | ≤ 100 | N/A |
Water for Injection (WFI) | ≤ 1.1 (20°C) | ≤ 500 | ≤ 10 | ≤ 0.25 | ||
Japan | JP (Japanese Pharmacopoeia) | Purified Water (PW) | ≤ 1.3 (25°C) | ≤ 500 | ≤ 100 | N/A |
Water for Injection (WFI) | ≤ 1.1 (20°C) | ≤ 500 | ≤ 10 | ≤ 0.25 | ||
China | ChP (Chinese Pharmacopoeia) | Purified Water (PW) | ≤ 2.0 (20°C) | ≤ 500 | ≤ 100 | N/A |
Water for Injection (WFI) | ≤ 2.0 (20°C) | ≤ 500 | ≤ 10 | ≤ 0.25 | ||
India | IP (Indian Pharmacopoeia) | Purified Water (PW) | ≤ 1.3 (25°C) | ≤ 500 | ≤ 100 | N/A |
Water for Injection (WFI) | ≤ 1.1 (20°C) | ≤ 500 | ≤ 10 | ≤ 0.25 |
Key Points:
- Conductivity: A measure of the water’s ability to conduct electricity, indicating the presence of ionic impurities.
- TOC (Total Organic Carbon): Reflects the amount of organic compounds present in the water.
- Microbial Limits: Specifies the maximum allowable microbial count to ensure the water is free from harmful microorganisms.
Endotoxins: Specific to Water for Injection, measures the permissible levels of bacterial endotoxins to prevent pyrogenic reactions.
What are the processes of pharmaceutical water treatment?
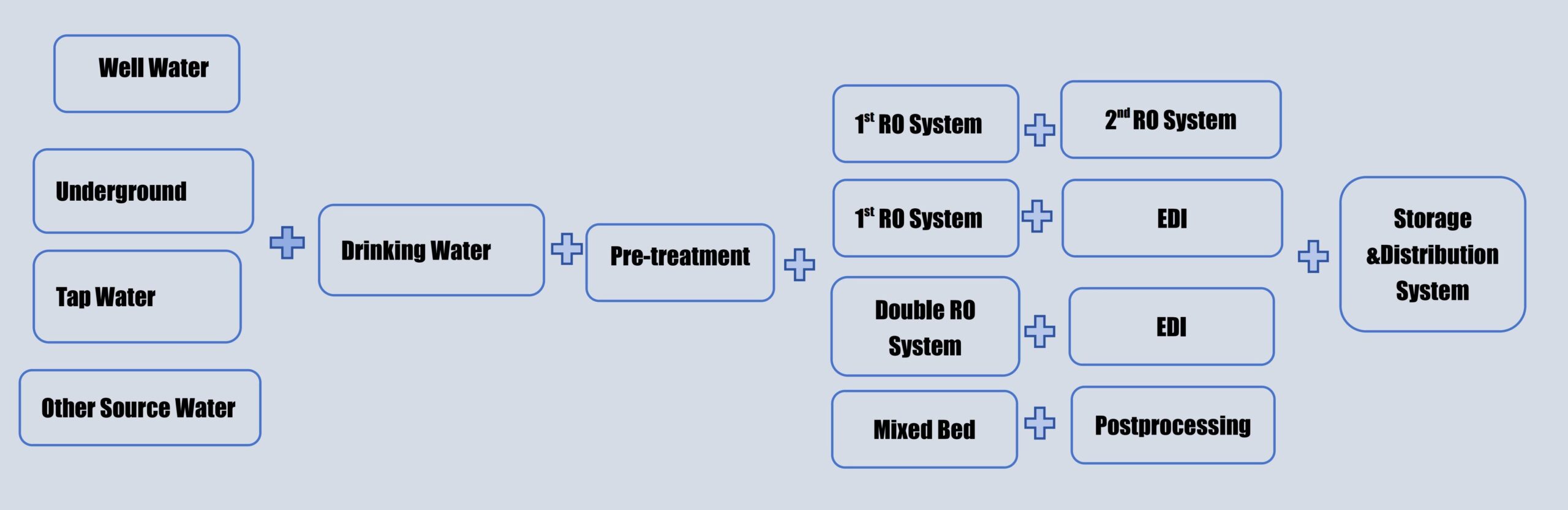